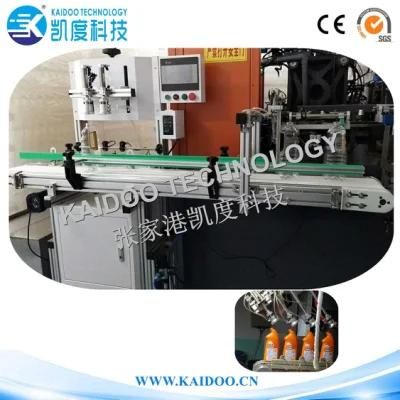
Leak Tester /Leak Detector (Four head)
ZHANGJIAGANG KAIDOO PLASTIC TECHNOLOGY CO., LTD.- Max Diameter of Workpiece:<500mm
- Mass Scope of Workpiece:<900kg
- Type:Compression Testing Machine
- Maxcapacity:<1000KN
- Accuracy Grade:0.5
- Load Way:Electronic Load
Base Info
- Model NO.:KDLT-4
- Loading Method:Dynamic Load
- Display:Digital
- Control:Computer Control
- Weight:0-100Kg
- Power Source:AC220V
- Oil Cylinder Position:Under
- Transport Package:Wooden Box
- Specification:10ml--10Liter
- Trademark:KAIDOO
- Origin:China
- HS Code:9031809090
- Production Capacity:500sets,Year
Description
Basic Info.
Model NO. KDLT-4 Loading Method Dynamic Load Display Digital Control Computer Control Weight 0-100Kg Power Source AC220V Oil Cylinder Position Under Transport Package Wooden Box Specification 10ml--10Liter Trademark KAIDOO Origin China HS Code 9031809090 Production Capacity 500sets/YearProduct Description
LEAK TESTER (MODEL: KDLT-4)KDLT series Leak Tester are used in the detection of plastic containers and iron container that for the industries of foodstuff, chemicals,medicine packing.

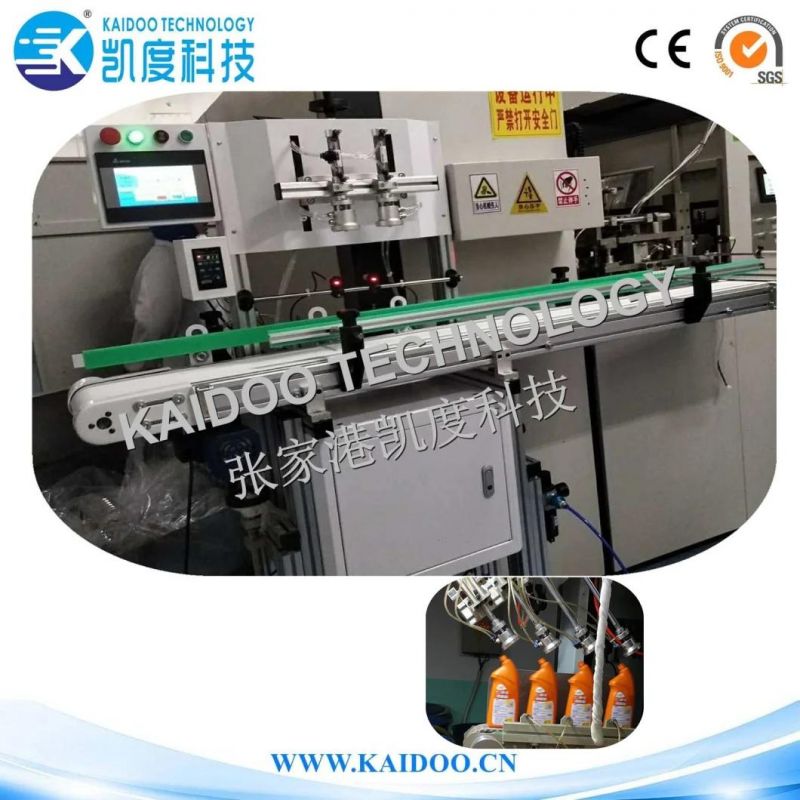
Main Characters of Leak Tester
Using PLC and Man-machine Interface,which is easy to operate. The Leak Tester are equipped with the high nicety pressure transducer, and use the differential micro-pressure logical analytical control method,high-accuracy and high-stability. The tiny and important leak could be detecter, it has high speed of detection, low error rate. The whole frame adopt European standard Aluminium alloy and it featuredby compact construction, pleaing shap, portable and endurable. It also can be customized according to customer specific requirements.
Why do we need to use Leak Tester ?
Before inventing leak testers, container producers usually used water-immersion bubble test method to detect leaks on containers. The real sensitivity is strongly influenced by many external factors,such as illumination codistions,water turbidity,unit location and placement, and water movement, which cann't guarantee good accuracy of detection. In addition, Containers need to be dried after being tested.
The invention of pressure decay test now provides a better solution to solve the problem. The application of leak tester in line with containers maker (Blow molding machine etc.) is able to determine the leak containers before filling, reducing unnecessary losses. A leak tester can test more than two containers each time, therefore improving the productivity greatly.